SURFACE INSULATION RESISTANCE TESTING
Below are the most common Surface Insulation Resistance / Electrochemical Migration testing methods that we perform.
Surface Insulation Resistance (SIR)
- Method 2.6.3.3 (85C / 85% Relative Humidity, 50 and 100 VDC biases, 168 hours, periodic monitoring)
- Method 2.6.3.7 (40C / 90% Relative Humidity, 25 VDC / mm bias, 168 hours, continuous monitoring)
Electrochemical Migration (ECM)
- Method 2.6.14.1 (IPC version of Bellcore Telcordia GR-78-CORE testing
- Actual GR-78-CORE specification
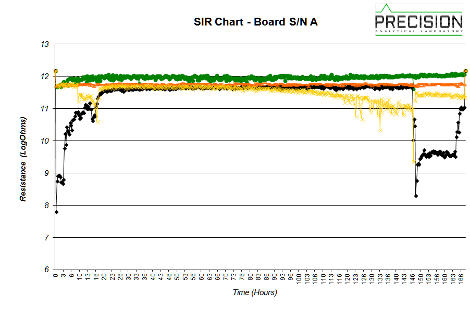
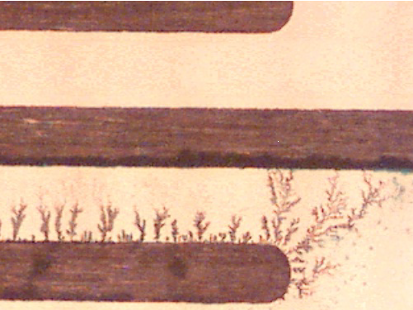
COMMON TEST VEHICLES EVALUATED
- IPC-B-24
- IPC-B-25
- IPC-B-25A (Typically used for ECM testing)
- IPC-B-36
- IPC-B-52
- CSL / Foresite Umpire
- SMTA Saber
- Client specific test boards
FREQUENTLY ASKED QUESTIONS
Below are the two most frequently asked questions posed by our clients on the subject of SIR and ECM testing. If you have questions on the subject of SIR / ECM that you would like to see our answers to on our site, please contact us.
Q1. What is SIR and ECM testing and are the two tests similar or different?
A1. SIR stands for Surface Insulation Resistance and ECM stands for Electrochemical Migration. Both Surface Insulation Resistance and Electrochemical Migration tests are designed to determine the propensity for a material and/or process to lead to some sort of electrochemical event. Electrochemical events would include corrosion, electrical leakage and of course dendritic activity. Both procedures utilize a test board that is placed under specified environmental conditions with an applied test bias for a period of time. The period of time portion is really where the two tests start to diverge. In an SIR test, the duration of testing is typically 168 hours (7 days). The typical ECM test lasts 596 hours (25 days). Additionally, the two procedures generally have different measurement intervals. Older SIR test methods required measurements be taken at 24 hours, 96 hours and 168 hours. Newer SIR methods require frequent monitoring, which is currently defined at 20 minute intervals from the start of the test. The start of an SIR test is usually one hour after the boards have equilibrated to the specified test environment. In an ECM test, measurements are typically taken after the test boards have equilibrated at conditions for 96 hours and then again at the end of the test (21 days later). Both SIR and ECM seek to evaluate similar affects of materials and the processing of those materials on product function, but they definitely have differences in the way they are performed.
Q2. What are the factors that influence an electrochemical (ECM) reaction or event?
A2. Generally, most industry experts focus on three primary factors that are significant drivers for ECM events. However, in truth there are really five influencing factors, but two are secondary factors that we may have little control over. The three primary driving factors are as follows:
- An applied bias
- Some level of ionic contamination
- Some level of moisture
- Temperature
- Time (?)