Ion Chromatography Testing Services
TEST METHODS
Below are some of the ion chromatography testing methods that we typically perform:
- Method 2.3.28 (General Cleanliness Method for all Printed Boards and Printed Board Assemblies)
- Method 2.3.28.1 (Halide Determination Method for Soldering Fluxes, IPC-J-STD-004)
- Method 2.3.28.2 (General Cleanliness Method for Unprocessed Printed Boards, reference IPC-5704)
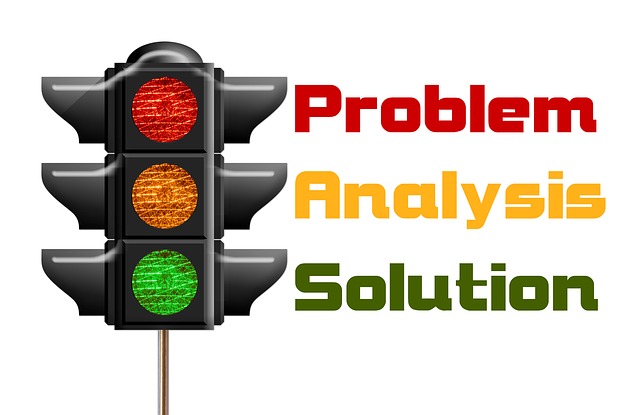
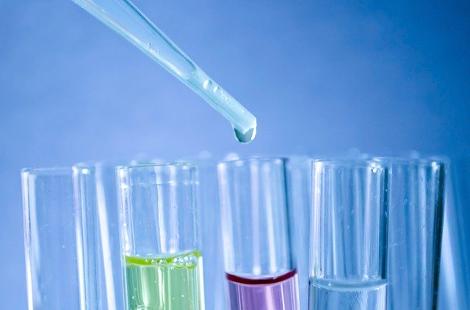
COMMON IONS WE ANALYZE
ANIONS INCLUDE:
- Fluoride (F-), Chloride (Cl-), Bromide (Br-), Nitrate (NO3), Nitrite (NO2-), Phosphate (PO43-) and Sulfate (SO42-)
CATIONS INCLUDE:
- Lithium (Li+), Sodium (Na+), Ammonium (NH4+), Potassium (K+), Magnesium (Mg2+) and Calcium (Ca2+)
WEAK ORGANIC ACIDS (WOA) INCLUDE:
- Adipic, Acetic, Citric, Formic, Maleaic, Succinic, and others
FREQUENTLY ASKED QUESTIONS
Below are the three most frequently asked questions posed from our clients on the subject of ion chromatography (IC) testing and cleanliness criteria.
Q1. WHAT IS ION CHROMATOGRAPHY (IC)?
A1. Simply stated, ion chromatography is an analytical tool that is used to identify and quantify the levels of ionic constituents that are within a liquid sample matrix. To apply this to the electronics industry, ion chromatography is used to evaluate the levels of different ionic contaminates that are found within the different materials and processes that are used to produce the final assembly. When used properly ion chromatography can play an integral role in understanding the impacts different ionic residues may have on product reliability and performance.
Q2. WHAT ARE THE DIFFERENT IONIC SPECIES AND WHAT IMPACTS DO THEY HAVE ON PRODUCT RELIABILITY?
A2. When analysts speak of ionic species we are referring to anions, cations and different organic acid ions. Anions are ions that have a net negative charge. Some the more common anions would include: fluoride, chloride, bromide, nitrite, nitrate, phosphate and sulfate . Cations are ions that have a net positive charge. The more common cations would include: sodium, lithium, ammonium, potassium, magnesium and calcium. All of these ionic contaminates can come from a number of different sources. Having an understanding of the materials and processes that being used for the production of electronic products is helpful in evaluating their origins and potential impacts on product reliability.
The organic acids that are commonly discussed in the electronics industry show up as anions and are referred to as weak organic acids (WOA's) because they are "weak" acids. Typically, we would expect them to come from flux materials. However, they might also be found in different plating bath chemistries or perhaps even found in newer hot air solder leveling (HASL) flux formulations. Some common weak organic acids that you may have heard of include: acetic acid, citric acid, formic acid, succinic acid and malic acid. Currently there are more than forty different organic acids that are used within the electronics industry.
The second portion of the question is a bit more difficult to answer. The simplest answer to the question of impact is “It Depends”. In general, there are certain anion residues that are known contributors to electrochemical failures. Electrochemical (ECM) failures include corrosion, electrical leakage and dendritic growth. The typical bad actors found at work in the ECM Theater would be chloride, bromide, sulfate and the various weak organic acid residues. Most industry research has focused primarily on those residues. Any one of these or a combination of these could have potentially devastating affects to assembly longevity under the “right” conditions. At this point, the “It Depends” part of our answer comes into play as there are a number of variables to factor into the equation in understanding the "right" conditions and how residues might impact end product reliability. This is a subject for a later discussion.
In terms of the cation residues, it has not been our experience that they lead to significant ECM failures as are usually seen with the anion residues mentioned previously. In our experience, excessive cation residues are more often process indicators. In other words, they indicate that a process may not be in control. Admittedly, the amount of industry research available on the impact of cation residues is minimal compared to the research available for anion residues and so less is understood about how this species of ions impact product reliability.
Q3. WHEN WILL THE INDUSTRY DEVELOP SOME IONIC CLEANLINESS PASS/FAIL REQUIREMENTS FOR PRINTED BOARD ASSEMBLIES AND UNPOPULATED BOARDS?
A3. I am going to address the second portion of the question related to bare boards first as the assembly criteria is far more complicated. In December of 2009 the industry published cleanliness criteria for bare boards based upon the work of Delphi Automotive. Delphi Automotive has had a long history of testing bare boards for their applications and that resulted in the development of ion chromatography criteria for the boards used in those applications. Those criteria were considered by other industry ion chromatography experts as reasonable starting points and they were eventually adopted into an IPC document called IPC-5704 which is entitled, “Cleanliness Requirements for Unpopulated Printed Boards”. Additionally, there are a few companion user guides available to assist with understanding the criteria found in IPC-5704. IPC-5701 is the "User Guide for Cleanliness of Unpopulated Printed Boards" and deals with how cleanliness issues should be addressed in purchasing documents. Next is IPC-5702, which is the "Guidelines for OEMs in Determining Acceptable Levels of Cleanliness of Unpopulated Printed Boards" and provides those persons responsible for developing criteria for unprocessed board cleanliness with guidance on what to consider. Finally, we have IPC-5703, the "Cleanliness Guidelines for Printed Board Fabricators" which provides a general guidance to board fabricators on items that can directly and indirectly affect cleanliness. All of these documents can be helpful in developing unpopulated board requirements for your own boards and applications.
Now to the first part of the question related to assemblies and establishing assembled board pass / fail cleanliness criteria. This has been a long debated area in the realm of cleanliness testing. Everyone is seeking the answer to that age old question of "How clean is clean enough?" Unfortunately, the answer is not a simple one. In short, there is no one-size-fits-all set of criteria that will address all of the assembly cleanliness concerns. You might be asking Why? First off, not all design applications are the same. High frequency applications may have very different cleanliness requirements than applications dealing with high voltage. That said, there is an element of cleanliness that needs to be sensitive to the application. Next we must consider all of the materials and processes that make the final assembly. This would include the materials and processes from board fabrication, to component fabrication, to the final assembly. All of these materials and processes can have their own specific chemical footprint that can work together to shorten the life of an assembly.
Next we need to consider the end-use environment. Is it controlled or uncontrolled? Will the assembly have any exposure to the outside elements? The combination of voltage, sufficient levels of ionic contamination and the presence of moisture can be a huge threat to the reliability of your assembly. All this said, developing a set of cleanliness criteria is a highly challenging endeavor and by the time such criteria would be developed it would likely be obsolete given the pace at which electronic designs, materials and processes change.
There are a couple rules of thumb that might be of help here. First, each assembly has its own threshold for how much residue it can tolerate. Simply stated some designs and applications require a higher level of cleanliness than others. The second rule of thumb is to treat cleanliness as a sliding scale of risk. In other words, the more contamination you have on your assembly the greater the risk for premature failure. Ultimately, the designer and assembler have to be responsible and diligent in determining what level of cleanliness is acceptable for their product(s). This can be time consuming, expensive and tedious work, but doing it may save time, more money and just the sheer aggravation of dealing with a product failure. Let's also not forget that a company's reputation is at stake when products fail. That aspect also has a cost.